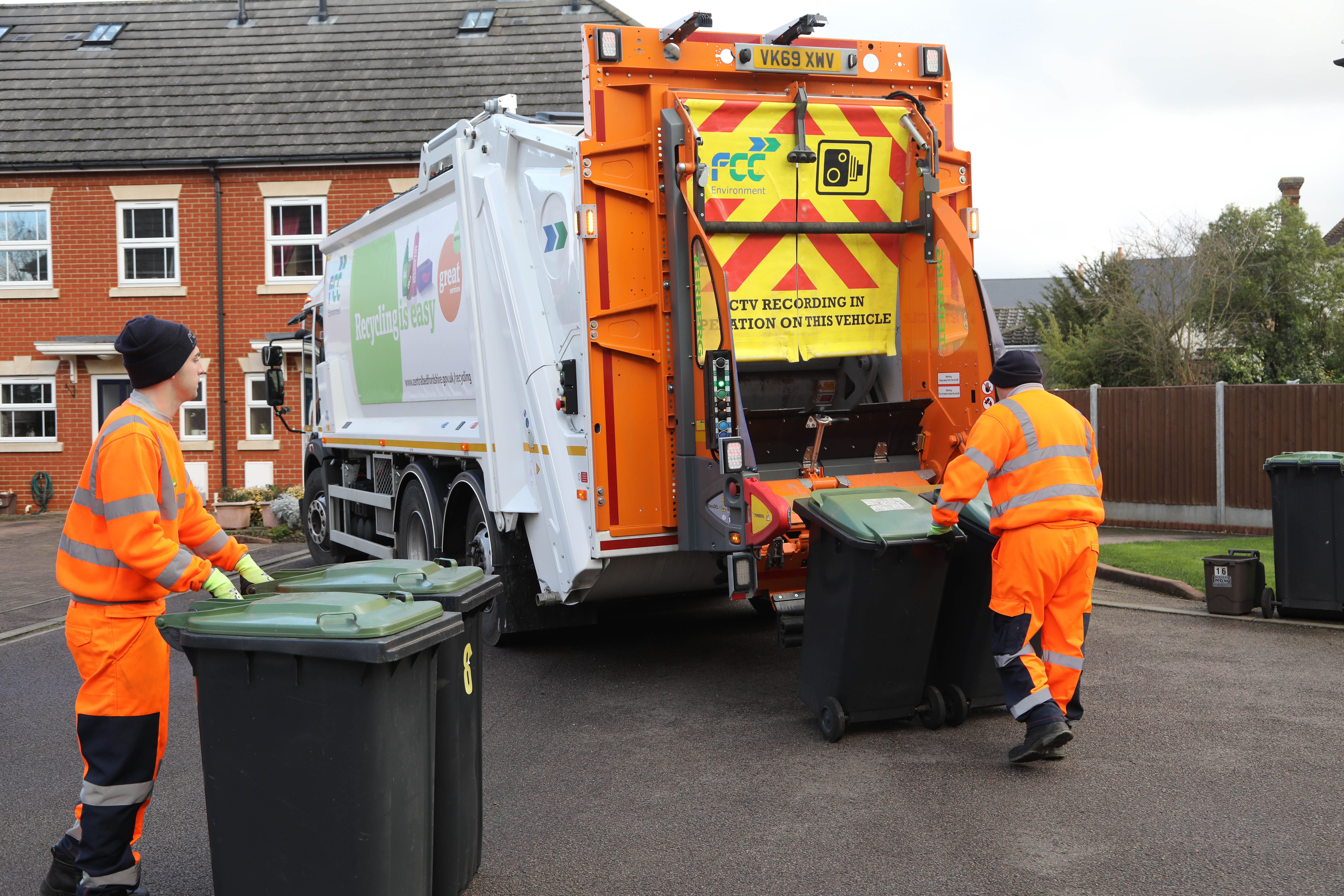
Contents
Every day, in sectors like waste and recycling, workers face hazardous situations that could — but don’t — result in harm. These are what we call near misses. Long seen as early warning signs, they’ve been widely used in health and safety culture for decades. But are we capturing the full picture? Or have we been missing crucial warning signals that modern technology now makes visible?
As data continues to become more widespread, perhaps it’s time to rethink what a near miss really is — and how we act on it.
What is a near miss?
A near miss is typically defined as an unplanned event that didn’t result in injury or damage but had the potential to do so. It’s a close call — a moment where things almost went wrong.
Good companies, with the right approach to keeping workers and members of the public safe, record incidents not accidents.
The well-known Safety Triangle model, from H.W. Heinrich and Frank Bird, tells us that for every serious accident, there are hundreds of near misses. The logic is simple: if we can learn from the small things, we can prevent the big ones.
But that assumes we know they’re happening — and that’s where the cracks begin to show.
Mind the reporting gap
Speak to any safety professional, and you’ll hear the same story: many or even most near misses go unreported. People may not realise how close they came to danger, may feel uncomfortable admitting it, or may just not have the time to report it. Worse still, some near misses are completely unseen. If no one witnesses them, they’re simply lost.
On paper, everything looks fine. But, in reality, it’s not.
Technology is now showing us what we’ve been missing.
Are the numbers misleading us?
Here’s the uncomfortable truth: traditional near miss reporting may no longer be enough.
When reporting relies solely on people noticing, remembering, and deciding to act, we leave too much to chance. Even in safety-conscious environments, underreporting is common — whether from time pressure, peer culture, or thinking “nothing really happened.”
As a result, managers may be making decisions based on false confidence. A site reporting no near misses may feel safe, but if that's because near misses aren’t being recorded, the risks haven’t gone — we’ve just stopped seeing them.
Seeing what was invisible
Technology is reshaping our understanding of risk. Systems like SiteZone’s RCV Smart Loader are exposing the real risk.
Prompted by the tragic fatality involving a loader in Coventry — although this incident did not involve them — FCC Environment wanted to get ahead of this kind of risk, so we worked in partnership to develop RCV Smart Loader. The system is designed to prevent a full bin lift if someone is detected in the danger zone at the rear of the vehicle.
During deployments, we’ve seen behaviour improve by up to 90% over short periods of time. Why? Because entering the danger zone triggers a delay — loaders are forced to reload, which they quickly learn to avoid. So, it creates a positive reinforcement of safe working practices.
It does more than intervene — it records every single incident of when an individual is in the danger zone.
When we analysed data from eleven operators — a mix of councils and commercial operator fleets — across 6,000 operational RCV days, we found that Smart Loader intervened 177,000 times preventing potential harm every 11 minutes. That means a loader was in the danger zone when the bin lift initiated. That’s potential for 1,000 near misses per minute across the UK’s fleet of RCVs. Arguably this comes from councils and operators that are at the forefront of best practice and looking to get ahead of regulation and requirements, so the figure could be even higher.
In the last issue of LAPV (Spring 2025) Chris Jones reported the HSE data that there were 500 serious injury incidents involving bin lifts in the previous 10 years. If we don’t intervene with these everyday near misses, then these serious injuries will not be reduced.
Where does a near miss begin
This raises a crucial question: at what point does a near miss become something more?
If someone steps into a clearly defined danger zone — especially when the lift could initiate automatically — shouldn’t that already be considered a near miss? Or even something more serious?
We believe the near miss begins the moment someone enters that no-go zone. That’s when the risk becomes real. It’s not just about the machinery moving — it’s about the potential for serious entanglement or being lifted with the bin. Waiting until someone is almost struck misses the point entirely. By then, it’s not a near miss — it’s a near tragedy [fatality].
A culture shift, powered by data
This isn’t about blaming individuals. Frontline workers operate in tough environments. But data doesn’t lie — it reveals patterns we can’t afford to ignore.
To move forward, we need a culture shift. One that goes beyond manual reporting and embraces the insights technology offers. It’s time to rethink what we count as a near miss — and act sooner. If the Boards and Management of operators, the Leaders of Councils and Authorities had real data would they make better decisions and keep workers safer?
The real question?
Near misses have long been a valuable tool in safety management. But in a world of data, we now see the risks that were once invisible.
If we don’t use that insight — if we continue relying on partial reports and outdated definitions — then we’re not protecting people as well as we could be.
At SiteZone, we’re seeing what happens when data brings these hidden dangers to light.
The real question is: now that we can see more, what will we do with it?
Because when safety is driven by data, we don’t just respond. We prevent the incident occurring.
See how Smart Loader works
About the Author – Gary Escott, Managing Director of SiteZone Safety
"While I wouldn’t call myself a traditional health and safety professional, I’ve worked for over 30 years in sectors where safety isn’t optional — from gas detection (both industrial and consumer), to construction, waste and recycling, and even as a frontline police officer. I’ve worked with chemicals where you don’t get a second chance — and I’ve seen what happens when things go wrong. That’s why I care deeply about helping people stay safe."